【蓋德化工網(wǎng) 化工財(cái)經(jīng)】近期國(guó)內(nèi)工業(yè)級(jí)85%甲酸市場(chǎng)行情呈上漲趨勢(shì),個(gè)別甲酸廠家裝置近期停車,無(wú)庫(kù)存,市場(chǎng)貨源稍有緊張,庫(kù)存不足。截至今日,國(guó)內(nèi)工業(yè)級(jí)甲酸周均報(bào)價(jià)為3722.22元/噸。
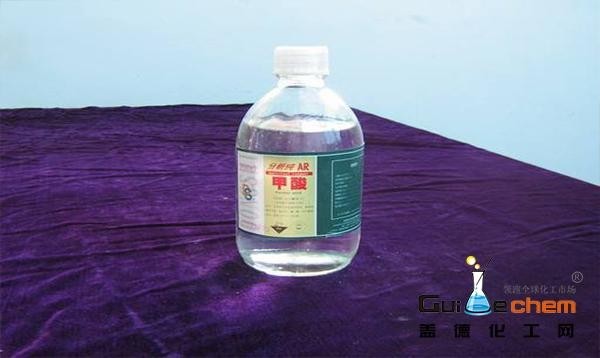
6月9日國(guó)內(nèi)部分地區(qū)甲酸市場(chǎng)總覽:
6月9日,山東榮悅化工有限公司85%甲酸含稅凈水價(jià)在4000元/噸,價(jià)格暫穩(wěn),銷售正常。
6月9日,上海羅頓精細(xì)化工有限公司甲酸(甲酸含量≥85%)報(bào)價(jià)在4200元/噸,價(jià)格暫穩(wěn),銷售正常。
6月9日,漳州市薌城三安化工有限公司85%甲酸報(bào)價(jià)在4300/噸,價(jià)格暫穩(wěn),銷售正常。
6月9日,晉州市金宏達(dá)化工有限公司85%甲酸凈水出庫(kù)價(jià)暫穩(wěn)于3700元/噸,銷售正常。
6月9日,淄博普利斯化工有限公司85%甲酸報(bào)價(jià)在4000元/噸,價(jià)格暫穩(wěn),銷售正常。
行情總結(jié):
目前國(guó)內(nèi)工業(yè)級(jí)85%甲酸市場(chǎng)以漲為主,企業(yè)價(jià)格小幅度上調(diào),上游產(chǎn)品支撐甲酸市場(chǎng),市場(chǎng)貨源稍有緊張,下游產(chǎn)品皮革、農(nóng)藥行業(yè)需求正常。因此有利好因素,預(yù)計(jì)短期內(nèi)國(guó)內(nèi)工業(yè)級(jí)85%甲酸市場(chǎng)小幅向好。